Ways of Reducing Emissions
Some users create systems that actually fight against themselves by using too much reducer, or the wrong speed reducer. Generally, people buy the cheapest thinner they can, which often is a very fast reducer and they end up overcompensating with an increased number of passes to try and get everything to flow together. More passes result in more VOCs. Often you also end up with orange peel on the surface because the fast solvent will not let the finish wet long enough to flow together and level. Check with your finish manufacturer for the correct solvent information. They know what reducer will make their finish give you the best results. When using the correct reducer you only need to add enough to get the finish to flow out and lay down. Any more than that, and it is a waste.
Check to see if you have the correct size fluid tip in the gun. Too small of a tip would also require you to over reduce the finish just to get it to lay down. Again, this also results in the finisher making multiple passes in an attempt to get a uniformly wet surface. Most equipment requires the addition of only a small amount of reducer, if any, to get the material to flow correctly. The majority of pre and post-cat finishes are designed to be sprayed out in 3-to-5 mil wet coats. By checking to make sure that the gun is set up properly and you are using the proper reducer, you will find it easy to flow out a nice wet coat without using an excessive amount of solvent. Once you have corrected the solvent and tip issue, the hard part will be breaking some old habits. Getting a finisher to adopt a new reduction and/or application schedule can sometimes be a daunting task.
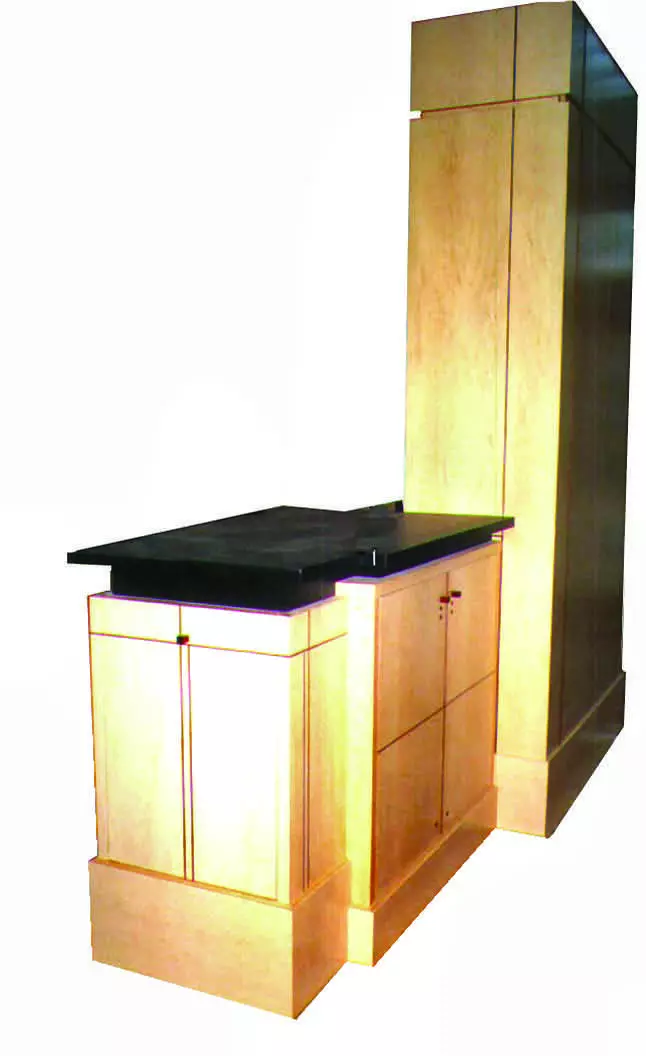
Use a higher solids finishing material. By using a conversion varnish that is 33% solids rather than a 25% solids precat lacquer, you can usually get by with two coats of finish instead of three, and put 40% less solvents in the air. This saves time, solvents, and big money.
Another solution is to use a different type of spray system. HVLP is more efficient than conventional systems, and Air Assisted Airless is more efficient than HVLP. The Air Assisted Airless system has several advantages. First, it requires less thinner in the finish to get good atomization. Second, the material comes out of the gun at 1/7th the speed that the material comes out of an HVLP gun; less speed, less material bouncing off the wood, means less overspray. Many surfaces can be coated with one pass, not 2 or 3. While the AAA system is fairly expensive, $2,500-3,000 per pump/gun, they increase your transfer efficiency. HVLP is about 65%, AAA is 80%. That is 15% less material being wasted as overspray. For a large manufacturer, the material savings alone pays for the equipment in a relatively short time. Again, the issue will be re-training the finishers to use the equipment the way it was intended to maximize results, and minimize problems.
The finisher is the key to the success of any system. Some might be easier to convince than others. I personally think “more experienced” finishers get stuck in their ways and get the attitude that “this has been working well for years, so why should I change it now”. My answer is that even a clock that is stopped gives the correct time twice a day. Regulations, materials, and technology change; requiring us to change. These changes are usually for our own benefit. Small changes can make big differences. Getting people to realize that change is good, is the hard part.